Why use copper rather than aluminium in power transformers?
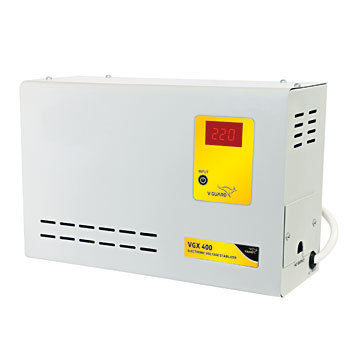
Power transformers are at the centre of all fashionable systems. While not electricity, the planet can’t run, and without transformers, the electrical system can’t be thought of.
Does one understand what is in the heart of these transformers?
Yes, you bought it right! It’s the windings of the transformers, without that they can’t work. These windings are either of Copper or aluminium. However, copper coil stabilizer for ac are most popular over the Aluminium windings as they’re higher and superior in several respects than them. Let’s discuss one by one what makes copper the most popular alternative to aluminium completely once it involves the transformers.
Why can we like Copper over aluminium in transformers?
1. Lower Creep Level:
Copper has abundant lower creep than that of aluminium. The creep rate of aluminium goes up to twenty five times below the acute loading and high-temperature conditions. This makes the aluminium wounded transformers additional liable to failures than that of copper wound transformers.
2. Sturdy and Long Terminations:
The copper terminations are durable and long-lasting than that of aluminium owing to the distinction within the formation of the oxides which forms throughout their life span. Oxide is soft and electrically conductive. It simply breaks down also. Whereas, the corundom is simply opposite of it. It’s tough because it got powerfully clanged to the terminals and is difficult to dislodge when it get shaped and accumulated. In particular, the aluminium oxide formed on the terminals are electrically insulating also. Aluminium needs a layer of tin, copper or nickel just in case you’re going for non-mechanical connections such as soldering, etcetera.
3. No Galvanic Action:
There’s no galvanic action in case of copper to copper terminations. Therefore, in the case of copper windings, the terminations made of the electrical devices allow copper to copper terminations at the transformer terminals. The connectors are commonly created up of copper or copper alloys reminiscent of brass etcetera therefore, there’s no danger of galvanic action throughout their terminations. Whereas, aluminium once in contact with copper or copper alloys during termination loses material through galvanic action and ends up in loosening of contacts or complete loss of contacts.
4. Harder, stronger and ductile:
Copper is way harder, stronger and ductile than aluminium and every one this lets copper expand less and does not let it flow at termination points. Thus preventing regular inspections and different maintenance such as modification connections or checking terminations. Aluminium being weaker flows aloof from the terminals once tightened and if not tightened properly, it ends up in loose connections, sparking. Even fireplace within the installations, if left unrestrained for extended durations.
5. High Short-Circuit withstand Capability:
Copper, compared to aluminium, has marvellous mechanical properties, reminiscent of yield strength or modulus of elasticity. This leads to completely going for copper wounded transformers when it involves transformers wherever short circuits chance is higher, such as arc furnaces. The frequent short-circuits deteriorate the systems and end up in the many weakening of electrical devices. Also their terminations, successively reducing the reliability of transformers and the entire system as such
6. Smaller and Lighter:
Copper wound transformers are smaller, lighter and compact than aluminium transformers of identical rating. The copper has low impedance compared to aluminium. It’s simply 0.6 times that of aluminium and just in case of going for the aluminium wound transformer than the cross-sectional of the conductor needed is 1.66 times more than that of copper. This results in overall larger size of everything no matter what is employed within the producing of the electrical devices reminiscent of transformer tanks, oil, core, contacts, insulation, etcetera and every one this semiconductor diode to a heavier. Bigger transformer which needs a bigger and stronger space for being installed.
7. Less Metal Fatigue:
The High Voltage windings just in case they’re created from copper are less at risk of metal fatigue than that of aluminium windings. Because the fatigue lifetime of the aluminium conductor is way less compared to it of copper. This made the aluminium transformers additionally prone to failures once the windings get loose over an amount of operation.
8. High performance:
The copper wounded transformers have higher performance, better potency and lower lifecycle value as they need lower energy losses and are expensive to the customers pocket instead of drilling a hole. Because it happens within the case of aluminium transformers, wherever the upkeep cost, operational cost, installation cost. Different running expenses are abundant more than that of copper wound transformers.
9. Higher Current Distribution:
This distribution in copper conductors is better than that of aluminium because of its higher physical phenomenon and metallurgic properties. This prevents non-linear hundreds from inflicting further losses as they are doing within the aluminium wounded transformers, creating copper wounded transformers choice.
10. More Cost Effective to Manufacture:
The copper wounded transformers are less expensive whereas producing aluminium ones owing to less material and cross-sectional of the conductor needed. It needs smaller machines and different facilities reminiscent of smaller powder coating set-up, smaller internal control labs, less storage area, etcetera required throughout manufacturing. Making it more viable to manufacture than that of aluminium wound transformers.
Also read:
Nosara Estates Reviews Advantages | Secret Advantages Of Renting Out Your Vacation Home